|
Extracting minerals from the earth safely and efficiently is
our core competency. For a mid-tier gold producer, IAMGOLD
is still a young company. We haven't lost that entrepreneurial
edge. We're driven to be great miners – to mine and process
ore as cost efficiently as we can. Towards that end we have
built a culture committed to continuous improvement and
excellence in execution.
Continuous improvement encompasses many elements
designed to improve the way we work. Its benefits are far
reaching, and a strong continuous improvement culture
forces you to regularly challenge the status quo. We use
sophisticated tools to determine optimum strategies for
mining our assets and improving the efficiency of our mining
processes. We are diligent about managing production costs
and implementing cost-control initiatives to increase
profitability. While profitability is a key focus, it must be
balanced with the need to protect our people, our
environment and the communities within which we operate.
We will never compromise our commitment to operating under
the Zero Harm framework. We demand strong, visible safety
leadership from our site management teams and conduct
rigorous training programs and reviews. This is essential to
make the workplace safer and to improve the ability to spot
and solve problems before they result in an incident.
IAMGOLD's first-rate continuous improvement program
fosters an environment where everyone works smarter,
harder and safer. That benefits all stakeholders.
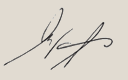
Gordon Stothart
Executive Vice President and Chief Operating Officer
Tools to Maximize Operating Efficiency |
Strategic Resource Development Planning (SRDP) enables mine planners to
assess various long-term strategies for mining resources based on limited drill data. It
works by generating a matrix of high-level "what-if" scenarios, with the preferred case
carried through to detailed analysis. By simulating the re-engineering of deposits to map
out the best ways to develop them, we can challenge assumptions and avoid tunnel vision
in our approach. At Rosebel, we applied SRDP to identify the optimal strategy to address
the increasing proportion of hard rock against a backdrop of a steadily increasing
resource. As a result, our long-term plan has been designed to optimize life-of-mine net
present value by investing in increased grinding capacity and incrementally expanding
the overall throughput capacity. This analysis can also help determine the appropriate
course of action when we experience a significant resource expansion or when there is
a significant change in gold prices. |
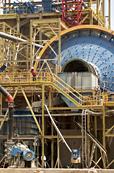 |
|
 |
Value Stream Mapping (VSM) is used to identify opportunities to improve an
operation from start to finish. The objective is to eliminate wasted time, wasted
material and wasted money. VSM works by creating a map of the process and
pinpointing problems with work flow, such as production bottlenecks. Once the
necessary changes are determined, a future map is generated to depict the
improved process. This enables us to lay out the required resources and the
timeline for executing improvements. It also ensures that we focus on improving
the steps in the value chain that will deliver the most meaningful improvement to
the process. The same mapping tool can also be applied at the micro level,
focusing on activities such as drilling and blasting. At Niobec, we used VSM to
match an increase in mill capacity with hoisting capacity. As a result, milling
capacity increased by 24%. |
|
Focusing on Margins
At IAMGOLD we monitor our margins closely. Given the nature of our business, they
are a more important performance metric than stand-alone cash costs. Higher costs
are correlated with higher gold prices. As prices rise, lower grades of ore become more
economical to mine. By mining these previously uneconomical portions of our resource
base we can optimize the ore deposit and extend the life of the mine. Although we
experience an increase in associated costs, we benefit from an increase in cash flow.
By understanding the correlation between gold prices and production costs, while
retaining operational flexibility, we can react accordingly to movements in the price of
gold to expand or protect our margins. |
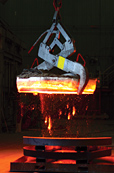 |
|
|
|
|
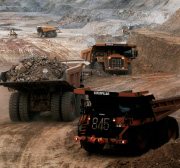 |
Rosebel – A Star Performer with Significant Expansion Potential |
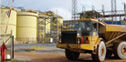 |
Producing 395,000 ounces of gold in 2010, the Rosebel mine has been a huge sucess. |
|
|
|
|
|
 |
|
|
Rosebel – A Star Performer with Significant Expansion Potential |
|
|
Producing 395,000 ounces of gold in 2010, the Rosebel mine has been a huge success. Since 2004, when the mine commenced operation, 2.7 million ounces of gold have been mined (on a 100% basis) and reserves grew by 3.7 million ounces to 6.2 million ounces as of December 31, 2010. With net reserve growth outpacing cumulative ounces of gold mined by 37%, the potential for continued grow is substantial.
Our focus going forward is on mine optimization. In 2010, we increased the number of leach tanks by 25% to a ccommodate a signifiant increase in throughput, the result of the previous year's mill expansion exceeding design capacity. This year, we are embarking on an aggressive expansion plan that is expected to increase annual production to 400,000 to 450,000 ounces. Spread out over the next seven years, we will invest a further $185 million in this program. With additional grinding capacity and mining equipment, we will be able to maintain mill throughput between 12 and 14 million tonnes per year, offsetting the impact of an ore mix trending towards a higher proportion of hard rock. The expansion will bring gold production forward in time and lower our long-term fixed costs by accelerating the rate of production. |
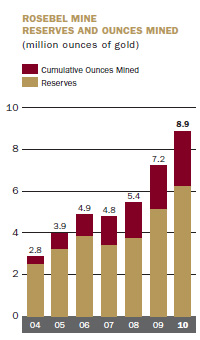 |
|
|
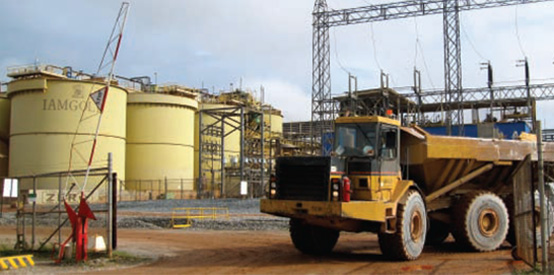 |
|
|
Essakane – Ramp Up
to Production with
Expansion Plans |
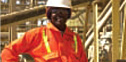 |
Essakane was the operating
highlight of 2010 |
|
|
|
|
|
 |
|
|
Essakane – Ramp Up to Production with Expansion Plans |
|
|
Essakane was the operating highlight of 2010. In the fourth quarter the mine produced 80,000 ounces of gold. Probable gold reserves at the end of the year were more than 4 million attributable ounces. We estimate that after the first three years of processing soft rock, there will be nine years of hard rock processing. A mine expansion feasibility study is underwayto demonstrate that by doubling hard rock processing capacity to 10.8 million tonnes, we would increase annual gold production from an estimated 315,000 ounces to 450,000 to 470,000 ounces. Pending the favourable outcome of the study, construction is expected to begin as early as the fourth quarter of 2011.
|
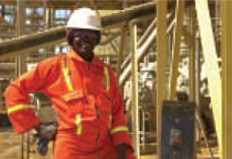 |
|
|
|
|
|